The key to a high-performance LiDAR lies in a spacious optical aperture. Our scanners provide flexibility with two aperture sizes and two scanning patterns (1D and 2D).
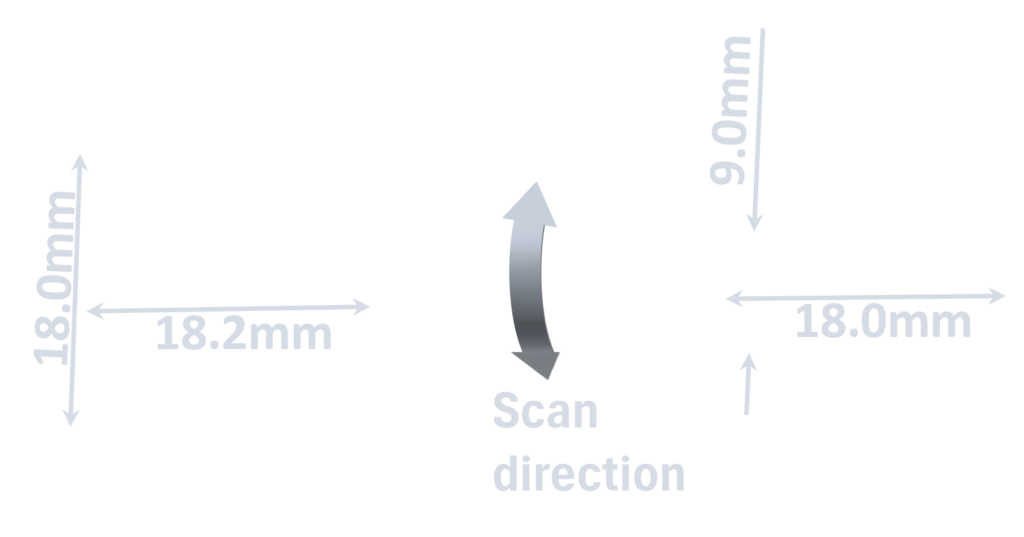
1D Scanner – Effective aperture 290mm2
Max optical scanning angle 20°@2kHz
1D Scanner – Effective aperture 150mm2
Max optical scanning angle 30°@2kHz
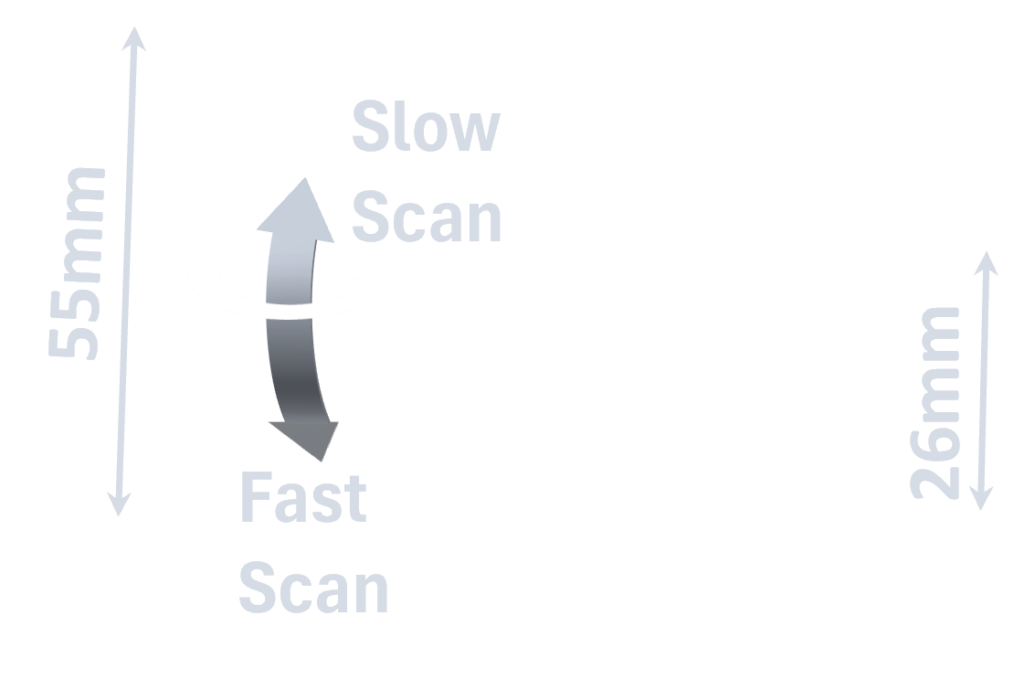
2D Scanner – Effective aperture 290mm2
Max optical scanning angle 80°(H)×20°(V)
2D Scanner – Effective aperture 150mm2
Max optical scanning angle 120°(H)×30°(V)
Reliability
Embark on the MEMS saga, where reliability tales oscillate between epic and tragic. Some emphasize the extraordinary reliability of MEMS devices, citing their pivotal role in critical life-or-death scenarios such as airbag deployment. Concurrently, skeptics highlight the perceived unreliability stemming from the use of silicon, a material likened to the fragility of glass. The twist? Both sides are onto something, and the secret lies in size. As size increases, so does the susceptibility to brittleness. Think about smashing a glass window, and then think about smashing a grain of sand.
Enter our star player—a legion of pint-sized MEMS mirrors defying the odds. Picture them enduring a rocky road, subjecting to vertigo-inducing accelerations (4G RMS, to be exact), the stability of our MEMS mirror shines through. A laser beam is projected onto the mirrors so that the stability of the MEMS mirrors can be observed though the reflected laser spot on the wall. Our MEMS behaves with an almost solid, unwavering composure, like a solid mirror slab. In stark contrast, large monolithic MEMS mirrors (but much smaller in total size compared to ours) succumb to pronounced influences, introducing considerable uncertainty in steering laser direction.
Post a rigorous 1500G shock test adhering to the AEC-Q100 automotive standard, our MEMS mirror emerges unscathed, showcasing unparalleled structural resilience.
Indeed, our products have successfully navigated through a series of rigorous automotive reliability assessments. During active operation, our products showcase exceptional resilience in various challenging conditions, such as the pothole shock test (GMW3172), random vibration test (ISO-16750-3), temperature oscillation (-40°C~125°C 100 cycles), high temperature and humidity (85 °C, 85% RH 1000h) and high temperature (125 °C 2000h).
The secret to this reliability? It lies in the art of keeping things small and nimble. Each mirror element remains compact and lightweight, ensuring a steadfast performance that defies the conventional trade-off between size and reliability. In the world of inSync, we prove that bigger and more reliable can be achieved at the same time.
Now - Let's rock it!
The slow-axis of the 2D hybrid scanning mirror is driven by an electromagnetic scanner which can follow arbitrary control waveforms. The demo above shows the 2D scanning mirror scanning 60° × 15° at 5 fps.
Typical scanning pattern
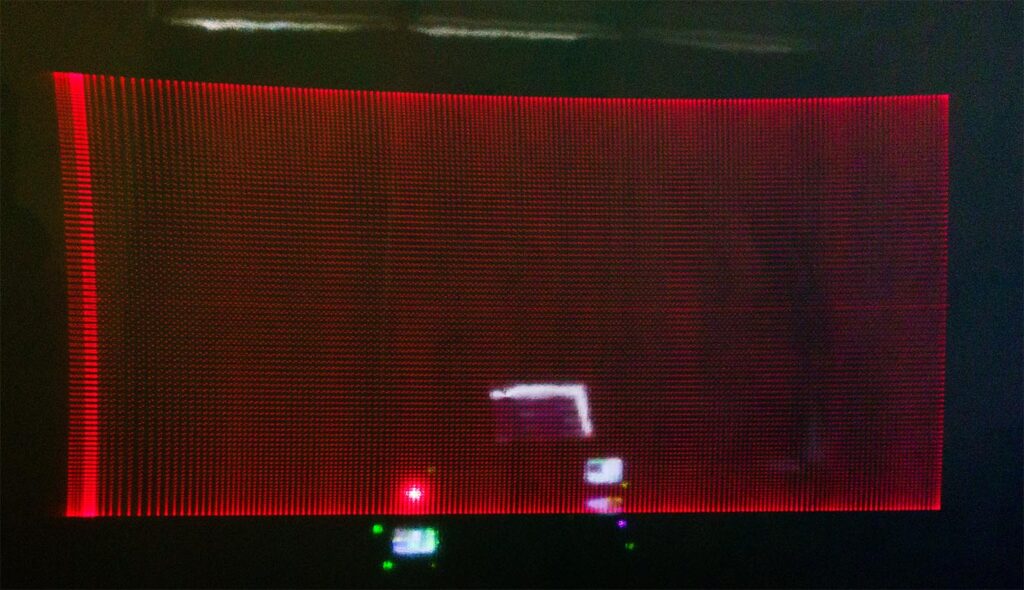
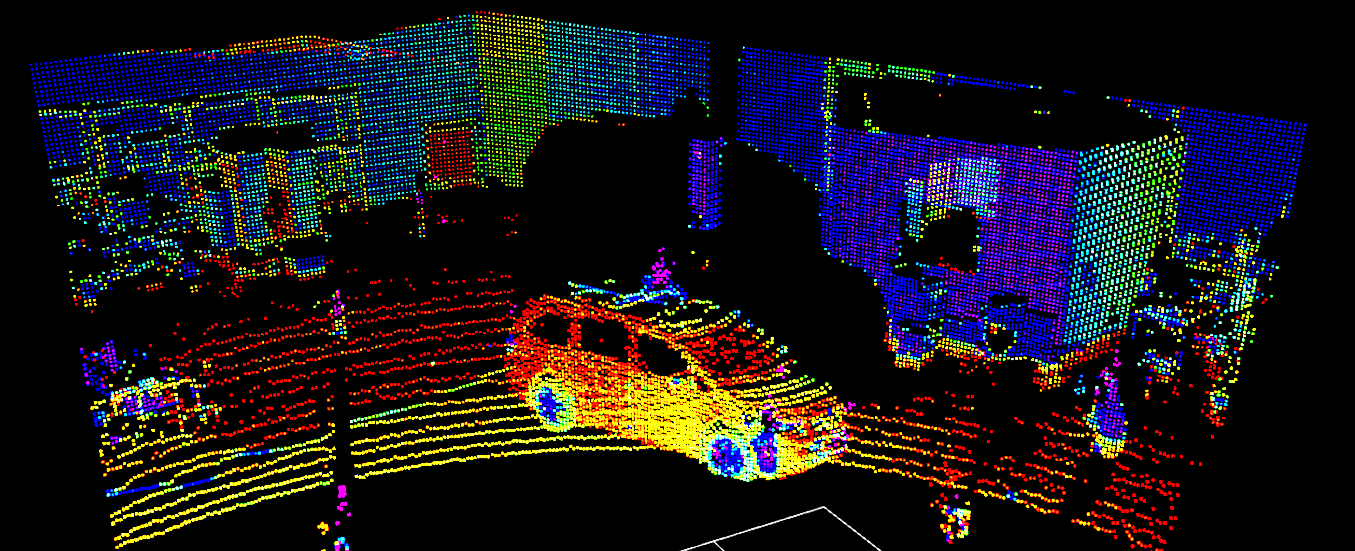
Reference LiDAR Design
The large aperture allows LiDAR to see further and clearer. As a demo, a reference LiDAR design with our MEMS scanning mirror can achieve resolution equivalent to a 250-line mechanical LiDAR with 200m effective range.