Large Aperture Scanner in a Small Package
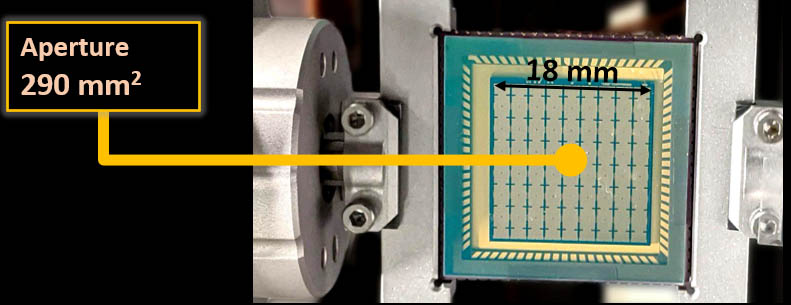
Synchronized micro mirror array synthesizes a large optical aperture.
See our product list.
Large Field-of-View by Hybrid 2D Scanner
Combining the power of MEMS technology and precision Galvo scanner, our hybrid 2D scanner covers an optical field-of-view of 120°(H)×30°(V), while being only 26 mm in height.
MEMS Scanning Mirror Array in Slow-Mo
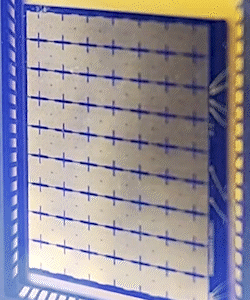
The MEMS Scanner scans at very high speed (2 KHz), which can only be resolved when played in slow-motion (1000x). Notice all the micro mirrors are moving in sync.
Unlike large monolithic MEMS mirrors, this light-weighted array of micro mirrors are extremely reliable (1500 g shock proof!), yet still provide large optical aperture. When used in applications such as Light Detection and Ranging (LiDAR), they can drastically improve performance and bring down the cost, (hopefully) bringing us one step closer to fully self-driving cars.
Why LiDAR?
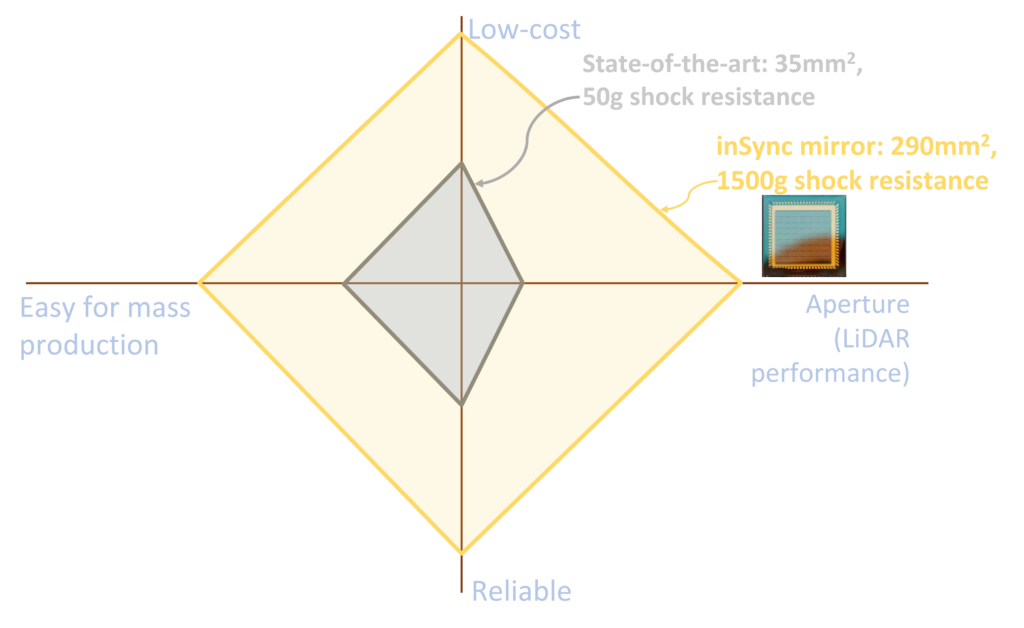
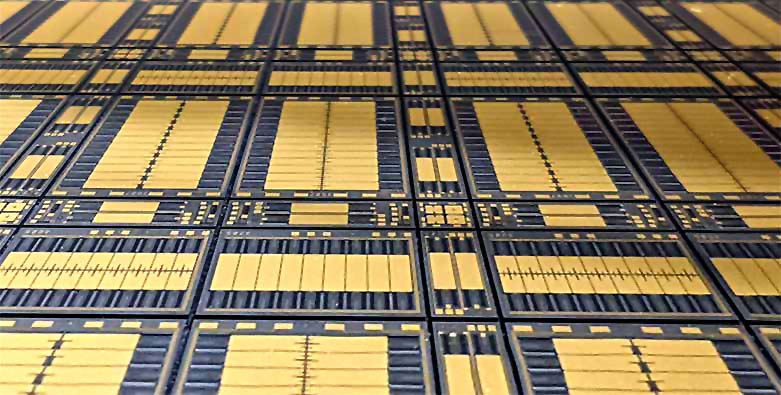
Even some greatest inventors of our time do not believe LiDAR should be in our cars. We agree – LiDAR on the market is either too expensive or lacks in performance. Why bother. Unless – What if LiDAR can be made cheap, reliable, compact, and of high performance? Here at inSync, we believe we found a way to do so.
The biggest obstacle to create the perfect LiDAR is the lack of the perfect scanner. For a long time, MEMS (Microelectromechanical Systems) technology is widely believed to be the key technology to achieve this. However, despite years of R&D, cheap, reliable, and large-aperture MEMS scanning mirrors do not yet exist. That is, until now. At inSync Mirror, we have adopted a unique approach to synthesize the largest effective optical aperture by perfectly synchronizing the movement of tens of tiny MEMS scanning mirrors.
inSync Mirror Powered LiDAR Architectures
Our 2D hybrid scanner provides the most convenient way of integrating inSync Mirror to your LiDAR system. Simply direct your laser TX/RX module directly towards the 2D hybrid scanner, and there you have it – a LiDAR! For optimal results, here are a few technical recommendations for the TX/RX module (Alert: we’re diving into technical territory below!).
We recommend utilizing an edge-emitting laser diode (EEL) with the fast axis oriented vertically and the slow axis horizontally. Aim for minimal divergence in the vertical direction, while allowing for a divergence of up to a few degrees horizontally, ensuring a uniform angle distribution. This setup enables a horizontally positioned 1D array of detectors on the RX side to capture multiple points of information from a single laser pulse. For instance, the TX/RX configuration of a 128-line LiDAR, where the TX laser spans 0.2° x 1.6° and the reflected laser is captured by a 1×8 SiPM array, is depicted in the illustration below (for more details and configurations such as a 256-line LiDAR, please contact us).
Our 1D MEMS scanner can complement other scanner types to achieve 2D scanning capabilities, given that our 2D scanner itself is a hybrid. For example, you can couple the MEMS scanner with a polygon scanner:
This arrangement does not require you to change the laser TX/RX module design, but may give you more design freedom.
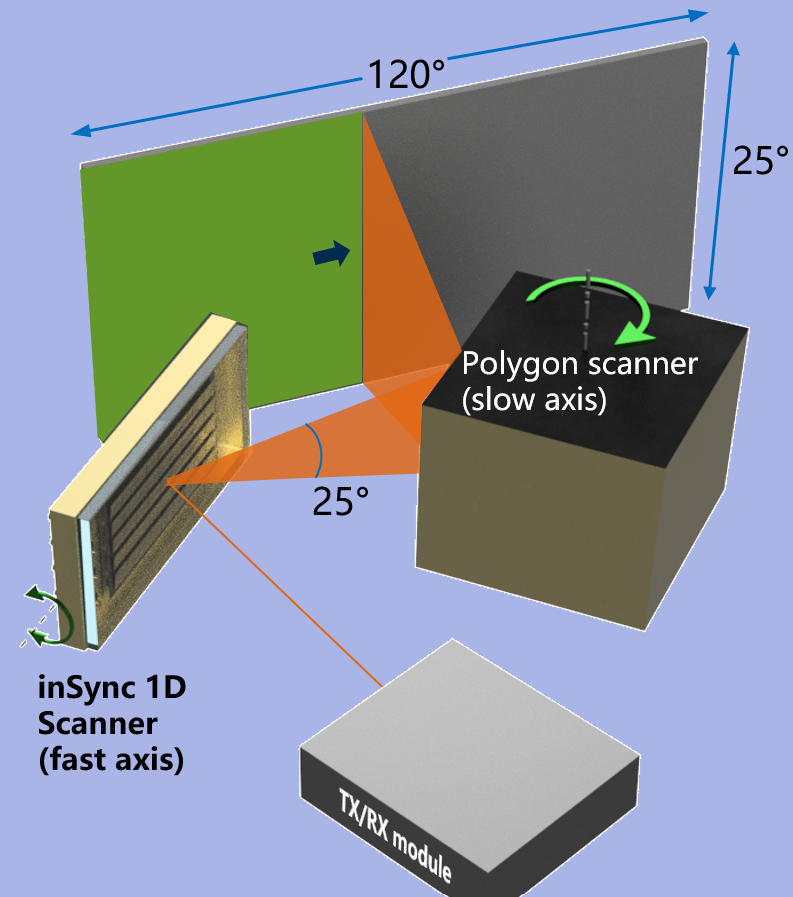
The use of inSync 1D MEMS scanner is versatile: you can even combine it with a polygon scanner with differently angled faces and get incredibly high-resolution LiDAR systems:
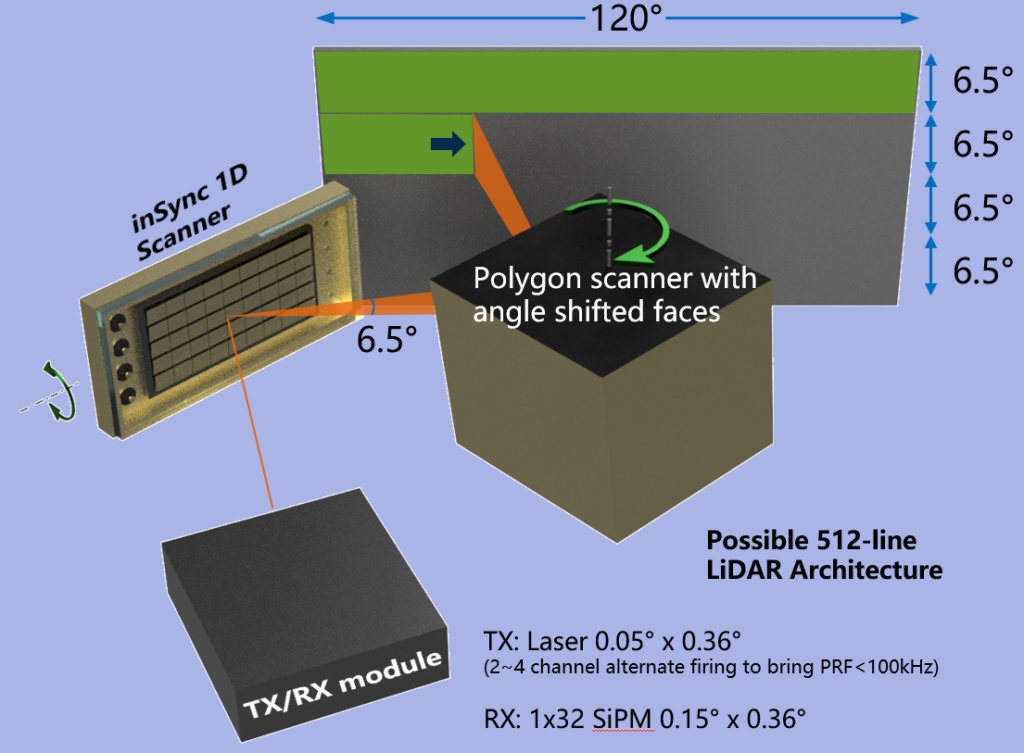
Using the design depicted in the illustration, you have the capability to assemble LiDAR systems with 512 lines of resolution or more, thanks to the recently introduced 1×32 SiPM detector array. Remarkably, you only need a single one of these arrays, all thanks to the scanning prowess of the inSync Mirror!
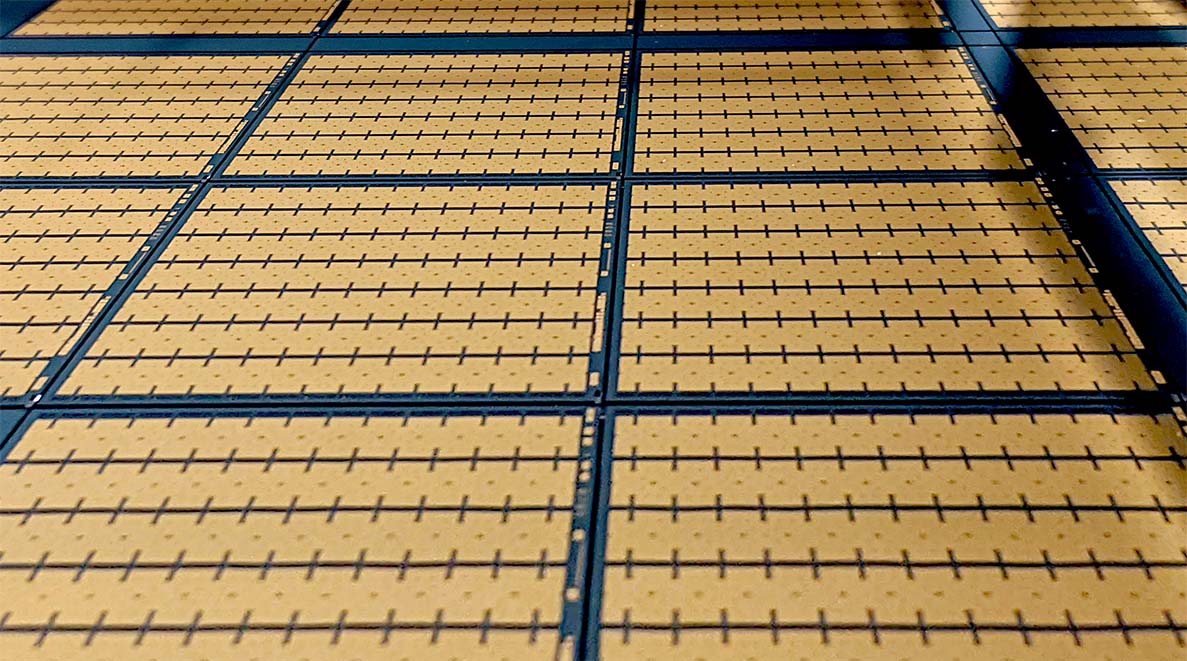
Foundry Standard Process
No special assembly or exotic materials. Very high mirror to die area ratio. All standard foundry process flow. The cost is significantly lower than the state-of-the-art.
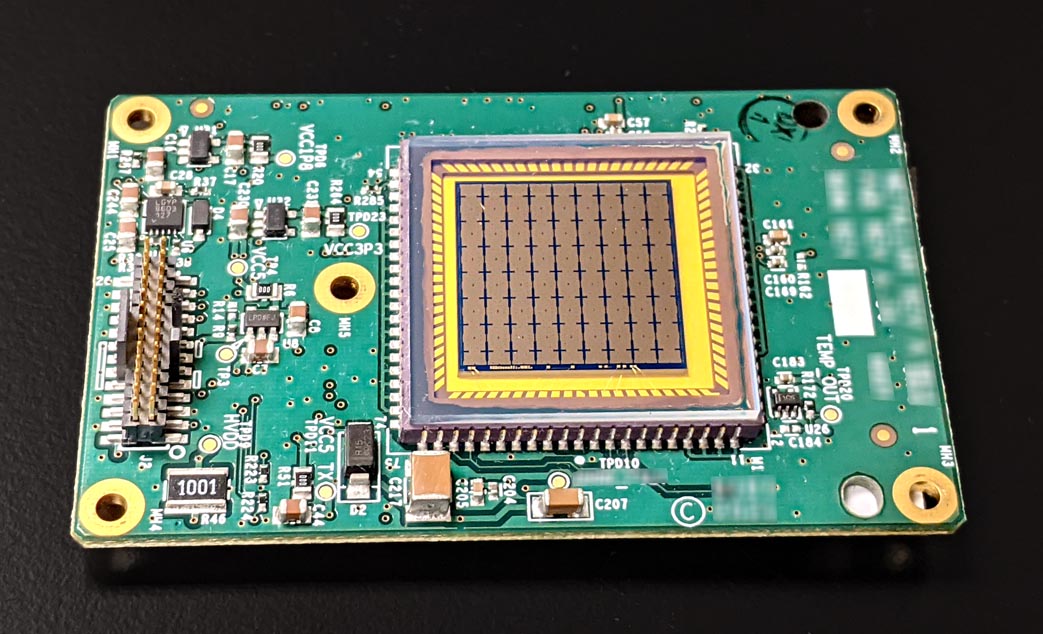
Complete Scanner Solution
In-house developed driving and sensing solution. Precise and reliable (passed AEC-Q100 vehicle standard). Evaluation kit available for close-loop control.
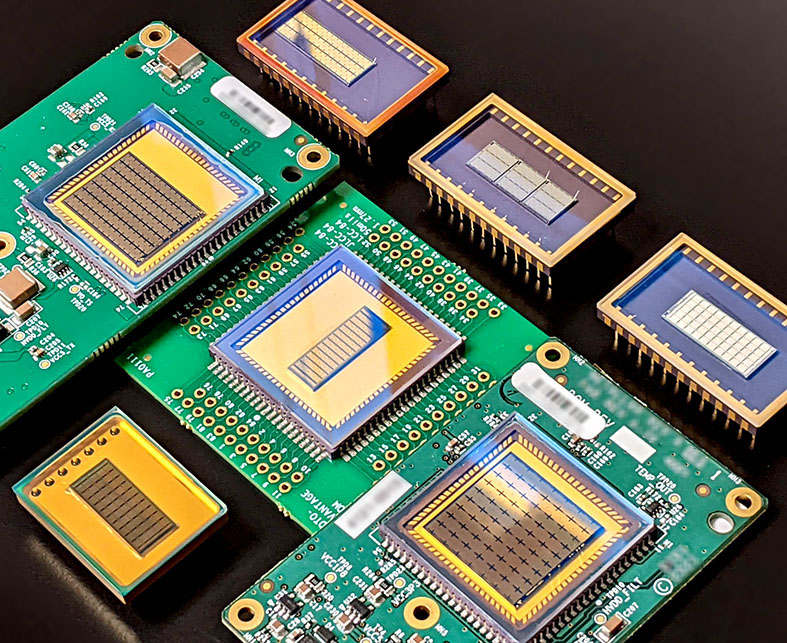
Easily Customizable
The aperture size, scanning frequencies, scanning angles and mirror coatings can all be easily customized to accommodate various application requirements.